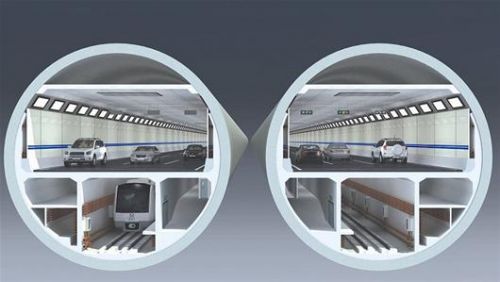
The Yangtze River, the longest in Asia, has been a hazardous natural obstacle for locals for thousands of years.
Splitting Wuhan in half, its span is approximately 1km at its narrowest point inside the city. While traditionally crossed by ferries, several permanent crossings, bridges and tunnels, now exist. And now a new crossing is to be added. A multipurpose tunnel combining road and rail transport will be built as part of Wuhan’s Metro Line Seven, and Sanyang Road, located in the city centre.
In August 2013 the National Development and Reform Commission approved the feasibility study for the first phase of Line Seven. This phase includes the Sangyang Road tunnel, which will run as a twin tunnel with tubes 2.5km long and an excavation diameter of 15.76m. The large diameter allows for an upper deck with a three-lane road, and a lower deck for the metro service, as well as safety and other electrical and technical networks.
The tunnel will be lined with precast segmental ring, forming an internal diameter of 13.9m, and an external diameter of 15.2m. The thickness of the segments is 650mm and they have a width of 2m. Each ring will be composed of 10 segments, comprising seven standard, two counter-key, and one key segment. The 30 static moulds were provided by CBE, which designed them in France and manufactured them in Yangling, China to reduce transportation costs.
CBE general director, Pascal Clerc added, “The complete mould design is based on the technical specifications and tolerances defined by our customer – a local precast company, as is often the case in China – and are confidential. But regarding the design and fabrication process, there really is no difference between this project and other large diameter tunnels, such as the Alaskan Way project, which we also supplied. In addition, the multi-function nature has no influence on segment or mould design. The ring is as it would be in any other‘classic’tunnel.
“However, every project is unique and we do individual pre-project studies regarding the specific design, taking into consideration dimensions, accessories and equipment such as sockets, shear cones, guiding rods etc. We pay special attention to the quantity of vibrators and their distribution at every project.” The local precast company uses a vacuum system to demould the 28,000 segments required by the project, which are then placed in a water basin during the later curing process. Gaskets are traditionally glued, as cast-in-place technology is not yet applied in China.